Reliability & PM Services
Reliability Work
Reliability Centered Maintenance and Reliability Centered Installations should be the standard in industry. However, many contractors are not well-versed in these concepts. One major cornerstone of IRR’s culture is reliability based work.
Reliability Centered Maintenance
Reliability Centered Installations
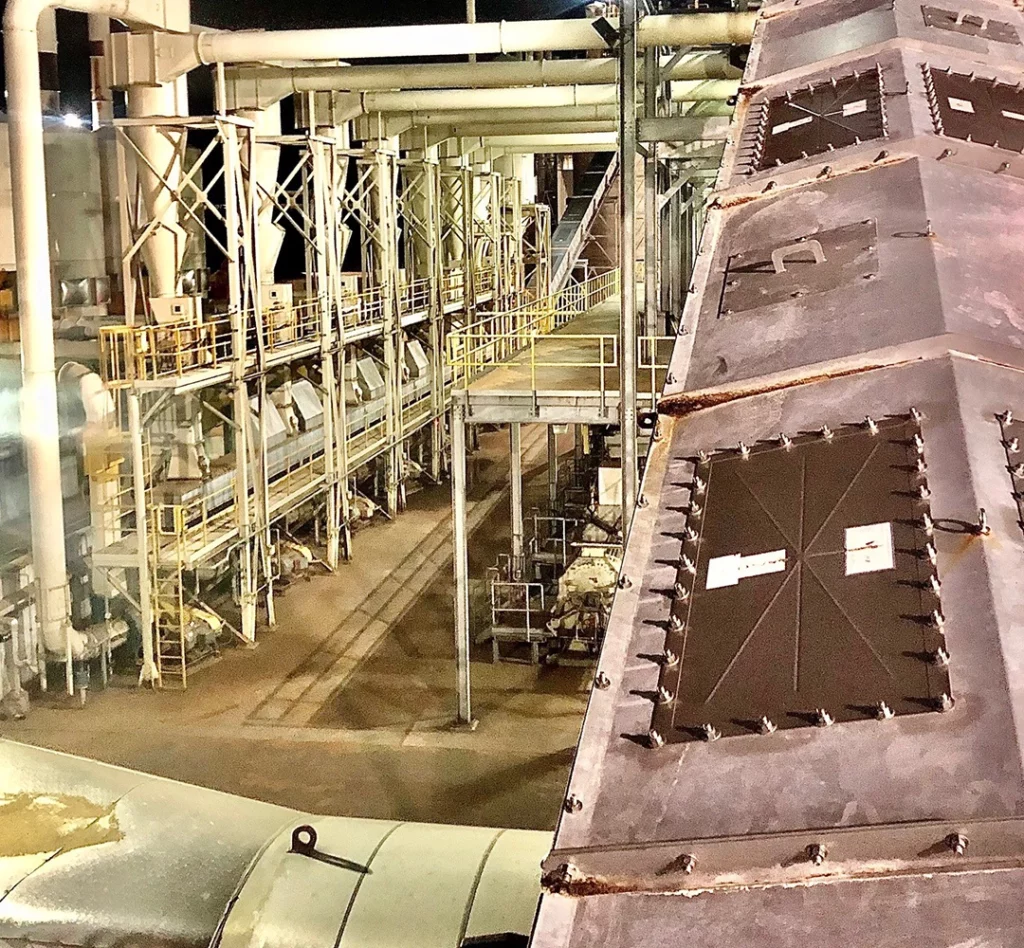